Химия - Сульфатный процесс - Общая характеристика сульфатного процесса
28 февраля 2011Оглавление:
1. Сульфатный процесс
2. Термины и определения сульфатного процесса
3. История
4. Общая характеристика сульфатного процесса
5. Химия сульфатной варки целлюлозы
6. Технология сульфатной варки целлюлозы
Свойства и особенности сульфатной целлюлозы
Свойства сульфатной целлюлозы определяются физико-химическими процессами сульфатной варки, а также условиями и длительностью её проведения.
По сравнению с сульфитной целлюлозой, сульфатная целлюлоза содержит меньшее количество легкогидролизуемых гемицеллюлоз и значительное количество пентозанов. В ней меньше смолистых и минеральных веществ, жиров; она имеет более низкую кислотность. С другой стороны, из-за своего коричневого цвета, сульфатная целлюлоза требует более сложной отбелки, кроме того её выход при равной степени провара на 3—4 % меньше.
У сульфатной целлюлозы более высокие бумагообразующие свойства: её волокна более гибки, она обладает лучшими механическими показателями. Бумага из неё более плотная, термостойкая, менее подвержена деформации. В то же время, именно эти свойства затрудняют набухание и размол сульфатного волокна при переработке.

Продукция, изготовленная из сульфатной целлюлозы, обладает лучшими диэлектрическими свойствами, что используется для производства электроизоляционных видов бумаг.
Сульфатная целлюлозы выпускается, обычно, в следующих видах:
- целлюлоза сульфатная хвойная небелёная — предназначена для производства высокопрочных тарных и упаковочных видов бумаги и картона, электротехнической бумаги, картонов технического назначения;
- целлюлоза сульфатная небелёная из смешанных пород древесины — используется по аналогии с хвойной целлюлозой;
- целлюлоза сульфатная хвойная белёная — предназначена для производства высококачественной бумаги для печати, письма и рисования; этикеточной бумаги, пергамина, бумаги-основы санитарно-гигиенического назначения, топлайнера, полиграфических бумаг и картонов;
- целлюлоза сульфатная белёная из лиственной древесины — предназначена для производства бумаги-основы для фотобумаги, фильтровальной бумаги, декоративной бумаги-основы для облицовочных материалов, в композициях писчей и печатной бумаги, бумаги-основы санитарно-гигиенического назначения, полиграфических бумаг и картонов;
- целлюлоза сульфатная пергидролизная — предназначена для производства вискозных кордных и технических нитей и высокомодульных волокон.
Сравнительные показатели сульфатного процесса
Доминирующее положение сульфатного процесса по сравнению с другими способами варки, помимо высоких прочностных характеристик сульфатной целлюлозы, объясняется следующими преимуществами:
- более низкие требования к породному составу и качеству древесного сырья; использование лиственной и хвойной древесины, а также, отчасти, древесных отходов;
- малое время варки;
- отработанные процессы регенерации тепла и варочного раствора, минимизация отходов, а также производство ценных побочных продуктов.
В качестве недостатков отмечаются:
- образование характерных дурнопахнующих газовых выбросов;
- невысокий выход целлюлозы;
- тёмный цвет небелёной целлюлозы и трудности её последующей отбелки;
- высокие первоначальные капитальные затраты на новое производство.
Сравнительная характеристика различных процессов варки целлюлозы приведена в таблице:
Метод | pH процесса | Активный катион | Активный анион | Температура варки, °C | Время варки, часов | Выход, % |
---|---|---|---|---|---|---|
Кислаясульфитная варка | 1—2 | H, Ca, Mg, Na, NH4 | HSO3 | 125—145 | 3—7 | 45—55 |
Бисульфитная варка | 3—5 | H, Mg, Na, NH4 | HSO3 | 150—170 | 1—3 | 50—65 |
Двухстадийная сульфитная варка стадия 1 стадия 2 |
6—8 1—2 |
Na Na, H |
HSO3, SO3 HSO3 |
135—145 125—140 |
2—6 2—4 |
50—60 |
Трёхстадийная сульфитная варка стадия 1 стадия 2 стадия 3 |
6—8 1—2 6—10 |
Na Na, H Na |
HSO3, SO3 HSO3 OH |
120—140 135—145 160—180 |
2—3 3—5 2—3 |
35—45 |
Нейтрально-сульфитная варка | 5—7 | Na, NH4 | HSO3, SO3 | 160—180 | 0,25—3 | 75—90 |
Щёлочно-сульфитная варка | 9—13 | Na | OH, SO3 | 160—180 | 3—5 | 45—60 |
Натронная варка | 13—14 | Na | OH | 155—175 | 2—5 | 50—70 |
Сульфатная варка | 13—14 | Na | OH, SH | 155—175 | 1—3 | 45—55 |
Сравнение сульфитного и сульфатного процесса по выходу целлюлозной массы для хвойной и лиственной древесины представлена ниже:
Компонент массы | Сульфитный процесс | Сульфатный процесс | ||
---|---|---|---|---|
Хвойная целлюлоза | Лиственная целлюлоза | Хвойная целлюлоза | Лиственная целлюлоза | |
Общий выход в том числе: |
52 % | 49 % | 47 % | 53 % |
Целлюлоза | 41 % | 40 % | 35 % | 34 % |
Глюкоманнан | 5 % | 1 % | 4 % | 1 % |
Ксилан | 4 % | 5 % | 5 % | 16 % |
Лигнин | 2 % | 2 % | 3 % | 2 % |
Экстрактивные вещества | 0,5 % | 1 % | 0,5 % | 0,5 % |
Общая схема производства целлюлозы сульфатным способом
Общая структурная схема производства целлюлозы сульфатным способом представлена на рисунке:
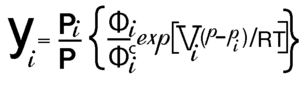

На первой стадии древесина проходит процесс подготовки, включающий в себя следующие операции:
- распиловка;
- окорка;
- рубка в щепу и последующая её сортировка.
Подготовленная щепа поступает на стадию варки. Варка сульфатной целлюлозы осуществляется непрерывным или периодическим способом в специальных варочных котлах большой ёмкости. В котёл вместе со щепой заливается варочный раствор, состоящий из белого щёлока и, частично, чёрного щелока от предыдущих варок. Начальная концентрация активной щёлочи составляет 50—60 г/дм³, конечная 5—10 г/дм³. Водородный показатель варки устанавливается не ниже 9—10. Гидромодуль варки: 4 и 2,5—3. Варка осуществляется при максимальной температуре 150—170 °C, давлении 0,25—0,80 МПа, в течение 1—3 часов в зависимости от характера исходного сырья и типа получаемой целлюлозы. В процессе варки осуществляются две сдувки: первая — терпентинная — идёт на получение скипидара; вторая — конечная — содержит, преимущественно, дурнопахнущие сернистые соединения. После отделения ценных органических продуктов, сдувочные пары направляют на установку утилизации тепла.

По окончании варки целлюлозная масса подаётся на стадию сортировки и промывки, при этом часть чёрного щелока отбирается сразу для подачи на выпарку. В процессе сортировки из целлюлозной массы отделяются твёрдые отходы. В ходе промывки отделяется разбавленный чёрный щелок, который частично поступает на стадию выпарки, а частично возвращается в варочный котёл для разбавления белого щелока. Сильно разбавленный чёрный щелок сбрасывается на очистные сооружения. Промытая целлюлозная масса в зависимости от назначения жидким потоком поступает на стадию сгущения для последующей отбелки, обезвоживания и прессования для получения товарной целлюлозы или дальнейшего отлива в бумагу или картон.
Перед стадией выпарки чёрный щелок направляется на фильтрацию для отделения волокна, а затем укрепляется уже упаренным щелоком до концентрации 22—24 % для уменьшения пенообразования при выпарке. После этого от чёрного щелока путём отстаивания отделяется сырое сульфатное мыло — тёмно-коричневая вязкая жидкость с характерным запахом. На 1 тонну целлюлозы его образуется примерно от 35—50 кг до 100—120 кг.
Выпарка щелоков происходит на многокорпусной вакуум-выпарной станции до концентрации сухого вещества 55—80 %. Упаренный щелок поступает на сжигание в содорегенерационный котлоагрегат.
Перед сжиганием к щелоку для возмещения потерь щелочи и серы в СРК добавляют свежий сульфат натрия. Под воздействием высокой температуры органические соединения сгорают, образуя углерод и углекислый газ. Углерод восстанавливает сульфат натрия до сульфида, а диоксид углерода реагирует со щелочью, образуя карбонат натрия:
При регенерации выделяется большое количество тепла и водяной пар.
Отметим, что в настоящее время существуют пилотные и лабораторные технологии, предполагающие в будущем совмещать регенерацию чёрного щелока с получением синтез-газа, который, в свою очередь, предполагается использовать для получения автомобильного биотоплива.
Твёрдый остаток после СРК растворяют в белом щелоке. Полученный раствор обладает грязно-зеленым цветом и называется зелёный щелок. В литературе не существует указаний на то, какие вещества в растворе обуславливают его зеленый цвет.
На следующем этапе зеленый щелок подвергают каустизации, добавляя известь:
Полученный белый щелок возвращают вновь на этап варки, а осадок карбоната кальция обжигают при 1100—1200 °C в известерегенерационных печах для получения извести:
Состав и характеристики варочного раствора
Основными компонентами варочного раствора перед началом варки являются гидроксид и сульфид натрия; также в значительно меньших количествах в состав раствора входят и другие натриевые соли: Na2CO3, Na2SO4, Na2SO3, Na2S2O3, Na2Sx, NaAlO2, Na2SiO3.
В процессе варки состав варочного раствора существенно меняется — концентрация активной щёлочи снижается практически в 10 раз, а в растворе появляются многочисленные органические соединения и натриевые соли минеральных и органических кислот. Вместе с тем, кислотность среды почти не меняется, так как поддерживается за счёт частичного и полного гидролиза солей натрия:
![]() |
![]() |
![]() |
![]() |
В зависимости от степени делигнификации, на 1 тонну целлюлозы образуется 7—10 м³ чёрного щелока, при этом массовая доля сухих веществ перед выпариванием в нём составляет 10—15 %. Плотность чёрного щелока перед выпаркой составляет порядка 1,05—1,10 г/м³, температура кипения 101 °C, вязкость 1,52×10Па·с.
Органические компоненты щелока составляют не менее 65 %. Среди них основные — лигнин, продукты разрушения поли- и моносахаридов, фенолы, органические кислоты, сераорганические соединения.
Типичная композиция белого щелока: | Пример состава чёрного щёлока: |
Соединение | Концентрация, г/литр | |
---|---|---|
в ед. NaOH | соединения | |
Гидроксид натрия | 90,0 | 90,0 |
Сульфид натрия | 40,0 | 39,0 |
Карбонат натрия | 19,8 | 26,2 |
Сульфат натрия | 4,5 | 8,0 |
Тиосульфат натрия | 2,0 | 4,0 |
Сульфит натрия | 0,6 | 0,9 |
Прочие компоненты | − | 2,5 |
Вся щёлочь | 156,9 | 170,6 |
Активная щёлочь | 130,0 | − |
Эффективная щёлочь | 110,0 | − |
Сульфидность | 47,1 | 19,7 |
Компонент | Содержание, % |
---|---|
Органические соединения | 78,0 |
Лигнин | 37,5 |
Сахарные кислоты | 22,6 |
Алифатические кислоты | 14,4 |
Жиры и смоляные кислоты | 0,5 |
Полисахариды | 3,0 |
Неорганические соединения | 22,0 |
Гидроксид натрия | 2,4 |
Гидросульфид натрия | 3,6 |
Карбонаты натрия и калия | 9,2 |
Сульфат натрия | 4,8 |
Прочие соли натрия | 1,0 |
Прочие соединения | 0,2 |
Просмотров: 8180
|